SPCS: Streamlining Construction Projects for Efficiency and Success
Introduction
In the dynamic and competitive world of construction, Strategic Planning for Construction Services (SPCS) has emerged as a cornerstone for driving project success. SPCS encompasses a comprehensive approach to project planning and execution, empowering teams to achieve optimal outcomes while navigating complex challenges. This guide delves into the intricacies of SPCS, unveiling its benefits, best practices, and practical implementation strategies.
Understanding the Significance of SPCS
The construction industry is characterized by intricate processes, diverse stakeholders, and ever-evolving technologies. SPCS provides a structured framework that enables teams to:
-
Enhance Communication: Establish clear lines of communication among all project participants, reducing miscommunication and delays.
-
Optimize Scheduling: Develop realistic project schedules that account for dependencies, resource availability, and potential risks.
-
Control Costs: Minimize project expenses through effective budgeting, procurement strategies, and change management practices.
-
Improve Quality: Ensure the delivery of high-quality construction outcomes by implementing robust quality control measures throughout the project lifecycle.
-
Increase Efficiency: Streamline project processes, eliminate bottlenecks, and maximize productivity through innovative tools and techniques.
Transitioning to SPCS: A Step-by-Step Approach
Implementing SPCS requires a systematic approach, involving:
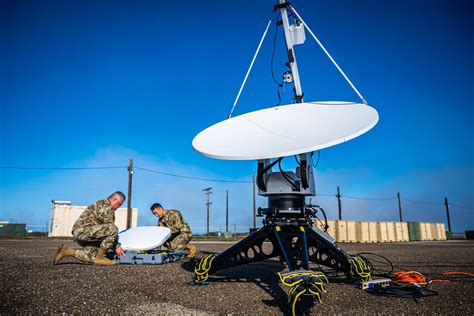
-
Define Project Objectives: Establish clear project objectives, including scope, budget, schedule, and quality targets.
-
Plan the Project: Develop a detailed project plan, outlining project milestones, activities, and responsibilities.
-
Manage the Project: Track project progress, identify and address risks, and make timely adjustments to ensure project deliverables are met.
-
Control the Project: Monitor project costs, change orders, and quality measures to ensure compliance with project objectives.
-
Close the Project: Document project accomplishments, lessons learned, and recommendations for future improvements.
Benefits of Embracing SPCS
Organizations that adopt SPCS enjoy tangible benefits, including:
-
Reduced Project Duration: Eliminate bottlenecks and optimize schedules, resulting in faster project completion times.
-
Lower Project Costs: Control spending through effective procurement, minimizing cost overruns and optimizing resource utilization.
-
Improved Project Quality: Implement stringent quality control measures, ensuring the delivery of high-standard construction outcomes.
-
Enhanced Client Satisfaction: Deliver projects on time, within budget, and to the desired specifications, fostering positive client relationships.
-
Increased Team Productivity: Streamline workflows, automate tasks, and empower teams to collaborate effectively, maximizing productivity.
Statistical Evidence Supporting SPCS Benefits
- A study by the American Institute of Architects (AIA) found that projects using SPCS experienced an average cost reduction of 12% and a schedule reduction of 10%.
- A survey by the Associated General Contractors of America (AGC) revealed that contractors employing SPCS reported 20% higher customer satisfaction ratings.
- Research conducted by the RAND Corporation indicated that projects managed with SPCS had a 60% lower likelihood of major project delays.
Best Practices for Effective SPCS Implementation
The successful implementation of SPCS hinges on adhering to best practices:

-
Engage Stakeholders Early: Involve all project stakeholders in the planning process to ensure buy-in and alignment.
-
Use Technology to Your Advantage: Leverage project management software, collaboration tools, and data analytics to streamline processes and enhance visibility.
-
Foster a Culture of Continuous Improvement: Encourage a proactive approach to identifying and addressing project challenges, promoting ongoing optimization.
-
Measure and Evaluate Project Performance: Track key performance indicators (KPIs) to assess project progress and identify areas for improvement.
-
Seek Professional Guidance: Consider consulting with industry experts to gain insights and implement best practices effectively.
Common Mistakes to Avoid in SPCS
Navigating the intricacies of SPCS requires vigilance in avoiding common pitfalls:
-
Lack of Planning: Inadequate planning leads to disorganization, delays, and cost overruns.
-
Poor Communication: Insufficient communication channels and ineffective communication strategies result in misunderstandings and conflicts.
-
Unrealistic Scheduling: Creating overly ambitious schedules that fail to account for potential risks and dependencies.
-
Insufficient Cost Control: Neglecting to monitor project costs and implement cost-saving measures can lead to budget overruns.
-
Lack of Quality Control: Compromising on quality standards can result in rework, delays, and diminished project value.
Comparing SPCS to Traditional Construction Management Approaches
SPCS stands out from traditional construction management approaches by:
Feature |
SPCS |
Traditional Approach |
Project Planning |
Comprehensive, involving all stakeholders |
Limited planning, often focused on short-term goals |
Scheduling |
Optimized, accounting for dependencies and risks |
Ad hoc, often based on intuition and experience |
Cost Control |
Rigorous, involving cost tracking and analysis |
Reactive, often relying on financial statements |
Quality Control |
Stringent, ensuring compliance with standards |
Variable, depending on individual contractor practices |
Stakeholder Engagement |
Proactive, fostering collaboration throughout the project |
Passive, often limited to contract negotiations |
Real-World Success Stories of SPCS
-
Case Study 1: A major hospital project implemented SPCS, reducing the project duration by 15% and saving $5 million in costs through optimized scheduling and procurement strategies.
-
Case Study 2: A commercial skyscraper utilized SPCS to enhance communication and coordination among the design team, contractors, and subcontractors, resulting in a 20% increase in productivity.
-
Case Study 3: A motorway construction project adopted SPCS to improve quality control processes, leading to a 60% reduction in rework due to defects.
What We Learn from These Success Stories
These success stories highlight the transformative impact of SPCS:

-
Embrace Collaboration: Encourage open communication and foster a collaborative environment to optimize project outcomes.
-
Leverage Technology: Utilize advanced tools to streamline processes, enhance visibility, and make informed decisions.
-
Focus on Continuous Improvement: Regularly evaluate project performance, identify areas for improvement, and implement innovative solutions.
Call to Action
To unlock the full potential of your construction projects, consider adopting SPCS today. By implementing best practices, avoiding common pitfalls, and embracing the benefits of SPCS, you can:
- Reduce project duration and costs
- Enhance project quality and client satisfaction
- Increase team productivity and efficiency
- Stay ahead of the competition in the dynamic construction industry
Consult with industry experts, invest in training, and equip your teams with the knowledge and tools necessary to excel in the world of construction. Embrace SPCS and transform your projects into resounding successes.
Tables
Table 1: Benefits of SPCS
Benefit |
Tangible Outcome |
Reduced Project Duration |
Faster completion times |
Lower Project Costs |
Minimized cost overruns |
Improved Project Quality |
High-standard construction outcomes |
Enhanced Client Satisfaction |
Positive client relationships |
Increased Team Productivity |
Maximized productivity and efficiency |
Table 2: Common Mistakes to Avoid in SPCS
Mistake |
Potential Consequence |
Lack of Planning |
Disorganization, delays, and cost overruns |
Poor Communication |
Misunderstandings and conflicts |
Unrealistic Scheduling |
Delays and resource wastage |
Insufficient Cost Control |
Budget overruns and financial instability |
Lack of Quality Control |
Rework, delays, and diminished project value |
Table 3: Comparing SPCS to Traditional Construction Management Approaches
Feature |
SPCS |
Traditional Approach |
Project Planning |
Comprehensive stakeholder involvement |
Limited planning and short-term focus |
Scheduling |
Optimized, accounting for risks and dependencies |
Ad hoc and experience-based |
Cost Control |
Rigorous cost tracking and analysis |
Reactive and financial statement-based |
Quality Control |
Stringent compliance with standards |
Variable and contractor-dependent |
Stakeholder Engagement |
Proactive and collaborative |
Passive and contract-negotiation-focused |