The Ultimate Guide to Grease Nipples: Lubrication Essentials for Optimal Machinery Performance
A grease nipple, also known as a zerk fitting, is an indispensable component in any lubrication system. It serves as the gateway through which grease is injected into bearings, joints, and other mechanical parts, ensuring their smooth operation and extending their lifespan. Understanding the importance, function, and proper use of grease nipples is crucial for maintaining the efficiency and reliability of your equipment.
Relevance and Benefits of Grease Nipples
Lubrication is the lifeblood of any mechanical system. Without it, friction and wear would rapidly deteriorate components, leading to premature failure and costly downtime. Grease nipples play a central role in lubrication by facilitating the delivery of grease to the exact points where it is needed.
The benefits of using grease nipples extend beyond the protection of individual components. They:
-
Reduce friction and wear: Grease creates a protective film between moving parts, minimizing friction and preventing metal-to-metal contact that can lead to damage.
-
Improve performance and efficiency: Well-lubricated machinery operates more smoothly and efficiently, reducing energy consumption and improving productivity.
-
Extend component lifespan: Regular greasing extends the life of bearings, seals, and other parts by protecting them from wear and corrosion.
-
Prevent catastrophic failures: By detecting and addressing lubrication issues early on, grease nipples help prevent catastrophic failures that can endanger personnel and damage property.
Types and Design of Grease Nipples
Grease nipples come in various types, each designed to meet specific application requirements. The most common types include:

-
Straight: These are the most common type and are used in most general lubrication applications.
-
Angle: Angled grease nipples are used in tight spaces where a straight nipple cannot be installed.
-
Hydraulic: Hydraulic grease nipples are used in high-pressure applications where a seal is required to prevent grease leakage.
-
Button head: Button head grease nipples are designed for use in confined spaces where accessibility is limited.
In terms of design, grease nipples typically consist of the following components:
-
Body: The main body of the nipple, which is typically made of metal or plastic.
-
Head: The head of the nipple is where the grease is injected. It can be straight, angled, or have a button design.
-
Valve: The valve inside the nipple prevents grease from leaking out when it is not in use.
Selecting the Right Grease Nipple for Your Application
Choosing the right grease nipple for your application depends on a number of factors, including:
-
Type of grease being used: Different greases require different types of nipples to ensure compatibility.
-
Pressure requirements: High-pressure applications require the use of hydraulic grease nipples.
-
Accessibility of lubrication point: Choose a nipple design that allows for easy access to the lubrication point.
-
Environmental conditions: Extreme temperatures or corrosive environments may require the use of specialized grease nipples.
Effective Greasing Techniques
To ensure that grease nipples are used effectively, it is important to follow proper greasing techniques:
-
Use the right grease: Consult with your equipment manufacturer to determine the correct type of grease for your application.
-
Clean the grease nipple: Remove any dirt or debris from the grease nipple before injecting grease to prevent contamination.
-
Apply grease slowly: Inject grease slowly and evenly to avoid overgreasing and damage to the nipple or the equipment.
-
Lubricate regularly: Establish a regular greasing schedule based on the equipment manufacturer's recommendations and operating conditions.
-
Monitor grease levels: Check grease levels regularly and add grease as needed to prevent under-lubrication.
Common Mistakes to Avoid
To avoid common pitfalls that can compromise the effectiveness of grease nipples, it is important to:
-
Avoid overgreasing: Overgreasing can cause damage to seals and bearings, and it can also attract dirt and debris.
-
Don't use the wrong grease: Using the wrong grease can damage the nipple and the equipment.
-
Neglecting maintenance: Failing to clean, inspect, and lubricate grease nipples regularly can lead to premature failure.
-
Ignoring environmental factors: Extreme temperatures or corrosive environments can damage grease nipples and reduce their effectiveness.
Step-by-Step Approach to Using Grease Nipples
-
Identify and locate the grease nipples: Determine the location of all grease nipples on your equipment.
-
Clean the grease nipple: Remove any dirt or debris from the grease nipple using a clean rag or compressed air.
-
Connect the grease gun: Attach the grease gun to the grease nipple. Ensure that the connection is secure.
-
Inject grease: Slowly and evenly inject grease into the nipple. Avoid overgreasing.
-
Disconnect the grease gun: Once the grease nipple is lubricated, disconnect the grease gun.
-
Wipe away excess grease: Use a clean rag to wipe away any excess grease that has spilled around the nipple.
Table 1: Recommended Greasing Intervals for Common Equipment
| Equipment | Greasing Interval |
|---|---|---|
| Electric motors | Monthly |
| Bearings | Weekly |
| Chains | Daily |
| Gears | Quarterly |
| Pumps | Monthly |
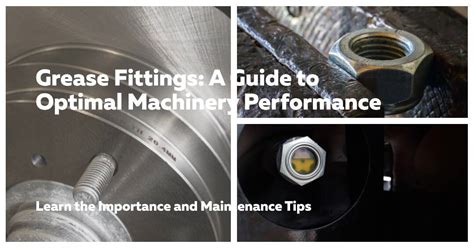
Table 2: Comparison of Grease Nipple Types
Type |
Advantages |
Disadvantages |
Straight |
Most common type |
Can be difficult to access in tight spaces |
Angle |
Suitable for tight spaces |
May not provide as secure a connection as straight nipples |
Hydraulic |
For high-pressure applications |
Requires specialized grease guns |
Button head |
For use in confined spaces |
Can be more difficult to clean and maintain |
Table 3: Troubleshooting Common Grease Nipple Problems
Problem |
Cause |
Solution |
Grease leakage |
Damaged or worn valve |
Replace the grease nipple |
Difficulty injecting grease |
Clogged grease nipple |
Clean the grease nipple using compressed air or a wire brush |
Grease nipple is loose |
Loose connection |
Tighten the grease nipple |
Grease nipple is broken |
Excessive force or damage |
Replace the grease nipple |