Thrust Washers: The Ultimate Guide to Specifying, Installing, and Maintaining
Introduction
Thrust washers, also known as thrust bearings, are critical components in a wide range of mechanical applications. Their primary function is to transfer thrust loads and prevent axial movement between mating surfaces. Understanding thrust washers and their proper usage is essential for ensuring the longevity and reliability of your machinery.
Types of Thrust Washers
There are several types of thrust washers, each designed for specific applications and load requirements:
-
Plain Thrust Washers: Flat, ring-shaped washers made from materials such as steel, bronze, or babbitt. They are suitable for low to moderate loads.
-
Tapered Thrust Washers: Have a tapered profile, allowing for axial adjustment. They can accommodate misalignment and heavy loads.
-
Ball Thrust Washers: Contain ball bearings between two hardened races. They provide high load capacity and low friction.
-
Roller Thrust Washers: Similar to ball thrust washers but use cylindrical rollers instead of balls. They offer even higher load capacity.
-
Self-Aligning Thrust Washers: Feature a spherical or cylindrical surface that allows for some misalignment.
-
Composite Thrust Washers: Made from a combination of materials, such as a steel backing with a plastic or composite facing. They provide high strength and wear resistance.
Materials for Thrust Washers
Thrust washers are primarily made from:
-
Steel: Durable and cost-effective for low to moderate loads.
-
Bronze: Provides good wear resistance and conforms to mating surfaces.
-
Babbitt: A soft alloy used for high-load applications and to prevent damage to mating surfaces.
-
Composite Materials: Offer a combination of properties, such as high strength, wear resistance, and corrosion resistance.
Specifications for Thrust Washers
When specifying thrust washers, consider the following parameters:
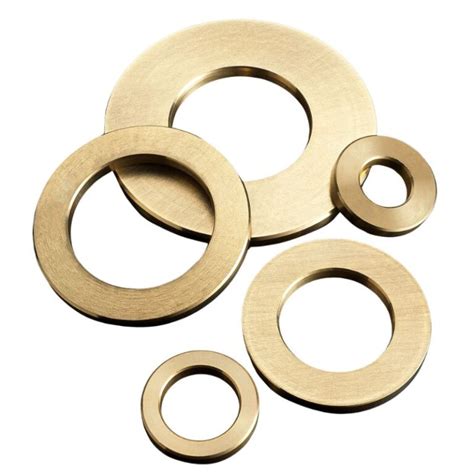

-
Material: Based on load requirements and desired properties.
-
Size: Inner and outer diameters, thickness.
-
Load Capacity: The maximum axial load the washer can withstand.
-
Speed: The maximum rotational speed at which the washer can operate.
-
Temperature Range: The operating temperature range for the washer material.
Installation of Thrust Washers
Proper installation is crucial for optimal performance:
-
Clean mating surfaces: Remove any dirt or debris.
-
Lubricate surfaces: Apply a thin layer of lubricant to reduce friction.
-
Position accurately: Ensure the washer is correctly aligned and centered.
-
Tighten uniformly: Use appropriate torque settings to avoid overtightening or loosening.
Maintenance of Thrust Washers
Regular maintenance extends the life of thrust washers:

-
Inspect regularly: Check for wear, damage, or misalignment.
-
Lubricate: Replenish lubricant as recommended by the manufacturer.
-
Replace when necessary: Replace worn or damaged washers promptly to prevent further damage to the mating surfaces.
Stories and Lessons Learned
Story 1: A manufacturing plant experienced premature failure of thrust washers in a high-speed application. Inspection revealed that the washers were made from the wrong material, causing them to overheat and fail.
-
Lesson: Choose the correct material for the application based on load, speed, and temperature requirements.
Story 2: A construction company faced excessive wear on thrust washers in a concrete mixer. Analysis showed that the washers were not properly lubricated, leading to increased friction and wear.
-
Lesson: Regular lubrication is essential to reduce friction and extend washer life.
Story 3: A power plant encountered vibration and noise issues in a turbine. Investigation found that the thrust washers were misaligned, causing uneven load distribution.
-
Lesson: Accurate alignment is crucial to ensure smooth operation and prevent premature failure.
Tips and Tricks
-
Use hardened washers: For heavy loads and high-speed applications.
-
Consider self-lubricating materials: To reduce maintenance requirements.
-
Use a step washer: To transition between different shaft diameters.
-
Inspect washers regularly: For signs of wear, damage, or misalignment.
-
Keep a spare set of washers: For quick replacement in case of failure.
Pros and Cons of Thrust Washers
Pros:
- High load capacity
- Prevent axial movement
- Reduce friction
- Protect mating surfaces
Cons:
- Can be expensive
- Require precise installation and maintenance
- May not be suitable for all applications
Call to Action
Thrust washers are essential components for reliable machinery operation. By understanding their types, materials, specifications, installation, maintenance, and tips, you can optimize the performance and longevity of your mechanical equipment. Stay tuned for further updates and insights on thrust washers.