Waterproof Bearings: A Comprehensive Guide to Enhancing Bearing Durability and Performance in Demanding Environments
Waterproof bearings are essential components in various industries and applications where exposure to moisture, liquids, and harsh operating conditions is unavoidable. They offer superior protection against water ingress, preventing premature failure and ensuring optimal performance and longevity of equipment. This guide delves into the fundamentals of waterproof bearings, their advantages, common applications, and effective strategies for their selection and maintenance.
Understanding Waterproof Bearings
Waterproof bearings are specifically designed to withstand exposure to water and other fluids while maintaining their functionality. They incorporate unique design features and materials that prevent water intrusion and preserve the integrity of the bearing components. These features include:
-
Seals: Waterproof bearings utilize specialized seals, such as lip seals, labyrinth seals, or contact seals, to prevent water ingress from external sources.
-
Coatings: The bearing surfaces and components may be coated with anti-corrosion coatings or materials to protect against rust, oxidation, and chemical degradation.
-
Lubrication: Waterproof bearings typically employ specialized lubricants that are resistant to water washout and maintain their lubricating properties even in wet environments.
-
Materials: Corrosion-resistant materials, such as stainless steel or ceramics, are often used in the construction of waterproof bearings to enhance their durability.
Advantages of Waterproof Bearings
-
Extended Bearing Lifespan: Waterproof bearings effectively minimize water damage, reducing corrosion, wear, and premature failure, resulting in a significantly extended lifespan compared to standard bearings.
-
Improved Reliability: Waterproof bearings ensure consistent performance and reliability in wet environments, preventing unexpected breakdowns or equipment malfunctions.
-
Reduced Maintenance Costs: By preventing water-related damage, waterproof bearings reduce the need for frequent maintenance and repairs, resulting in lower operational expenses.
-
Versatility: Waterproof bearings are suitable for a wide range of applications, including food processing equipment, marine environments, agricultural machinery, and industrial settings.
Common Applications of Waterproof Bearings
Waterproof bearings find extensive applications in industries where exposure to water or moisture is inevitable. Some common applications include:

-
Food and Beverage Processing: Waterproof bearings are crucial in food processing equipment, where they withstand frequent cleaning and exposure to liquids.
-
Marine Environments: Waterproof bearings are essential for marine applications, including propellers, rudders, and deck machinery, as they endure saltwater corrosion.
-
Agricultural Machinery: Waterproof bearings are used in agricultural equipment, such as irrigation systems, harvesters, and tractors, to withstand exposure to water and dirt.
-
Industrial Settings: Waterproof bearings are employed in industrial settings, including manufacturing, mining, and construction, where exposure to water, chemicals, or harsh operating conditions is prevalent.
Strategies for Selecting and Maintaining Waterproof Bearings
Effective Selection Strategies:
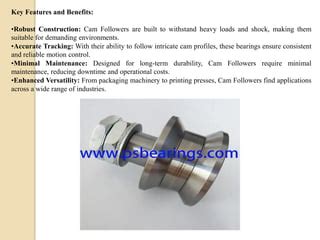
-
Application Environment: Determine the specific environmental conditions, such as water exposure, temperature, and load requirements, to select the appropriate waterproof bearing design.
-
Bearing Type: Consider the type of bearing required for the application, such as ball bearings, roller bearings, or thrust bearings, and ensure that it is compatible with waterproof designs.
-
Seal Type: Choose the appropriate seal type based on the level of water ingress protection required and the operating conditions.
-
Material Compatibility: Ensure that the bearing materials are compatible with the fluids or chemicals present in the application environment.
Effective Maintenance Practices:
-
Regular Inspections: Regularly inspect waterproof bearings for any signs of damage or water ingress, such as rust, corrosion, or lubricant leaks.
-
Proper Lubrication: Follow the manufacturer's recommendations for lubrication intervals and use water-resistant lubricants to maintain the bearing's integrity.
-
Cleaning: Clean waterproof bearings thoroughly to remove dirt, debris, and contaminants that could compromise their seal effectiveness.
-
Storage and Handling: Store and handle waterproof bearings properly to prevent damage and maintain their protective features.
Interesting Stories on Waterproof Bearings
Story 1: A food processing plant experienced recurring malfunctions of its conveyor belt system due to water damage on the bearings. After replacing the standard bearings with waterproof bearings, the malfunctions ceased, resulting in improved production efficiency and reduced downtime.
Story 2: A marine vessel operator faced constant bearing failures due to saltwater corrosion. By switching to waterproof bearings, they significantly extended the bearing lifespan, reducing maintenance costs and improving vessel reliability during offshore operations.
Story 3: A farmer struggled with premature bearing failure on his irrigation system due to exposure to water and dirt. Waterproof bearings solved the issue, extending the lifespan of the irrigation system and reducing costly repairs.


What We Learn from the Stories
- Waterproof bearings offer tangible benefits in applications where water exposure is a challenge.
- Proper selection and maintenance of waterproof bearings is essential for optimal performance and extended lifespan.
- Implementing waterproof bearings can lead to increased productivity, reduced downtime, and cost savings.
FAQs on Waterproof Bearings
-
What is the difference between a waterproof and a water-resistant bearing?
- Waterproof bearings provide complete protection against water ingress, while water-resistant bearings offer resistance to water but may not be fully submersible.
-
Can waterproof bearings be used in extreme temperatures?
- Yes, waterproof bearings are designed to withstand a wide range of temperatures, but the specific temperature range varies depending on the bearing design and materials.
-
How often should waterproof bearings be lubricated?
- Lubrication intervals for waterproof bearings are typically longer than for standard bearings, but it is important to follow the manufacturer's recommendations for specific applications.
-
How can I tell if a waterproof bearing has failed?
- Signs of waterproof bearing failure include noise, vibration, overheating, and reduced performance.
-
What are the best materials for waterproof bearings?
- Corrosion-resistant materials such as stainless steel, ceramic, or nitride-treated steel are commonly used in waterproof bearings.
-
Can waterproof bearings be repaired?
- Repairing waterproof bearings is not recommended as it may compromise their sealing integrity. In most cases, replacing the bearing is the best option.
Conclusion
Waterproof bearings are invaluable components in applications where exposure to water and other liquids is unavoidable. Their unique design features, such as seals, coatings, specialized lubricants, and corrosion-resistant materials, ensure exceptional protection against water ingress and extend the lifespan of equipment. By understanding the advantages, common applications, selection strategies, maintenance practices, and FAQs of waterproof bearings, you can make informed decisions that enhance the performance, reliability, and durability of your machinery in demanding environments.