Ceramic Bearings: A Comprehensive Guide
Introduction
Ceramic bearings are a specialized type of bearing that utilize ceramic materials in their construction, offering distinct advantages over traditional metal bearings. They exhibit exceptional durability, corrosion resistance, and smooth operation, making them ideal for demanding applications in various industries.
Benefits of Ceramic Bearings
Ceramic bearings provide numerous benefits, including:
-
High Hardness and Durability: Ceramic materials possess exceptional hardness, making ceramic bearings highly resistant to wear and abrasion. This durability extends the lifespan of the bearings, reducing maintenance and replacement costs.
-
Corrosion Resistance: Ceramic materials are inherently corrosion-resistant, making ceramic bearings ideal for applications involving harsh chemicals, liquids, or extreme temperatures.
-
Smooth Operation and Low Friction: Ceramic bearings exhibit low friction coefficients, resulting in smoother operation and reduced energy consumption.
-
High Speed Capability: Ceramic bearings can withstand higher speeds than metal bearings due to their lower friction and reduced heat generation.
-
Non-Magnetic Properties: Ceramic materials are non-magnetic, making ceramic bearings suitable for applications where magnetic interference can be detrimental.
Applications of Ceramic Bearings
Ceramic bearings find applications in a wide range of industries, including:
-
Medical and Surgical Equipment: The corrosion resistance and smooth operation of ceramic bearings make them ideal for medical devices such as surgical instruments and dental drills.
-
Semiconductor and Electronics: The high precision and low friction properties of ceramic bearings are essential for semiconductor manufacturing equipment and electronics devices.
-
Automotive and Aerospace: Ceramic bearings provide reduced weight, improved fuel efficiency, and increased performance in automotive and aerospace applications.
-
Industrial Machinery: Ceramic bearings offer durability and corrosion resistance in industrial machinery such as pumps, compressors, and conveyors.
Types of Ceramic Bearings
Ceramic bearings can be categorized into two main types:

-
Full Ceramic Bearings: These bearings utilize ceramic materials for both the races and balls, providing the highest level of hardness and durability.
-
Hybrid Ceramic Bearings: These bearings combine ceramic balls with metal races. They offer a balance of durability and cost-effectiveness.
Material Options for Ceramic Bearings
Ceramic materials used in bearings include:
-
Silicon Nitride (Si3N4): A high-performance ceramic with exceptional hardness and fracture toughness.
-
Zirconia (ZrO2): A tough and durable ceramic that offers resistance to wear and corrosion.
-
Aluminum Oxide (Al2O3): A cost-effective ceramic with good wear resistance and corrosion resistance.
Factors to Consider When Selecting Ceramic Bearings
Choosing the right ceramic bearing involves considering several factors:
-
Application Requirements: Determine the operating conditions, such as load, speed, and temperature, to ensure the bearing meets performance requirements.
-
Bearing Type: Decide between full ceramic or hybrid ceramic bearings based on the desired level of durability and cost.
-
Material: Select the appropriate ceramic material based on its hardness, fracture toughness, and other required properties.
-
Lubrication: Ceramic bearings may require specialized lubrication to minimize friction and wear.
-
Cost: Ceramic bearings typically have a higher initial cost than metal bearings, but their extended lifespan and reduced maintenance costs can provide cost savings over the long term.
Maintenance and Care of Ceramic Bearings
To ensure optimal performance and extend the lifespan of ceramic bearings, proper maintenance and care are essential:
-
Regular Inspection: Regularly inspect bearings for any signs of wear, damage, or contamination.
-
Proper Lubrication: Use the recommended lubricant and lubrication intervals to minimize friction and prevent premature failure.
-
Avoid Overloading: Operate bearings within their specified load capacity to prevent premature wear.
-
Cleanliness: Keep bearings and their surroundings clean to prevent contamination.
-
Storage: Store bearings in a dry and cool environment when not in use.
Common Mistakes to Avoid
Avoid these common mistakes to maximize the effectiveness of ceramic bearings:
-
Overgreasing: Excessive lubrication can attract contaminants and increase friction.
-
Incorrect Mounting: Improper mounting can cause premature bearing failure.
-
Material Mismatch: Using incompatible ceramic materials can lead to bearing damage.
-
Lack of Maintenance: Neglecting regular maintenance can shorten bearing lifespan.
-
Improper Handling: Mishandling bearings can cause damage to the delicate ceramic components.
Strategies for Effective Use of Ceramic Bearings
Implement these strategies to enhance the performance of ceramic bearings:
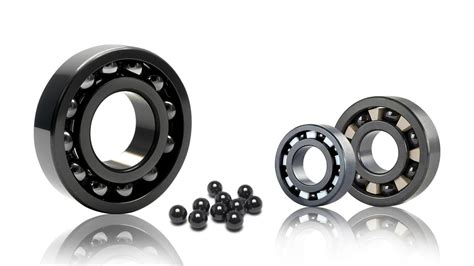
-
Use Specialized Lubricants: Select lubricants specifically designed for ceramic bearings to minimize friction and wear.
-
Optimize Mounting: Follow the manufacturer's recommendations for proper mounting procedures to ensure optimal performance.
-
Consider Hybrid Bearings: Hybrid ceramic bearings offer a cost-effective alternative to full ceramic bearings in less demanding applications.
-
Implement Regular Maintenance: Establish a regular maintenance schedule to inspect, lubricate, and clean ceramic bearings to extend their lifespan.
-
Train Personnel: Train personnel on the proper handling and maintenance of ceramic bearings to avoid damage or premature failure.
Conclusion
Ceramic bearings represent a significant advancement in bearing technology, offering exceptional durability, corrosion resistance, and smooth operation. Their unique properties make them ideal for demanding applications across various industries. By understanding the benefits, types, and factors to consider when selecting ceramic bearings, engineers and manufacturers can optimize their performance and maximize the efficiency of their equipment.
Table 1: Types of Ceramic Bearings
Type |
Composition |
Advantages |
Disadvantages |
Full Ceramic Bearings |
Ceramic races and balls |
Highest hardness and durability |
Higher cost |
Hybrid Ceramic Bearings |
Ceramic balls, metal races |
Balance of durability and cost-effectiveness |
Lower hardness than full ceramic bearings |
Table 2: Material Options for Ceramic Bearings
Material |
Characteristics |
Applications |
Silicon Nitride (Si3N4) |
High hardness and fracture toughness |
Medical instruments, semiconductor manufacturing |
Zirconia (ZrO2) |
Tough and durable |
Aerospace, automotive |
Aluminum Oxide (Al2O3) |
Cost-effective |
Industrial machinery, textile equipment |
Table 3: Applications of Ceramic Bearings
Industry |
Application |
Benefits |
Medical and Surgical Equipment |
Surgical instruments, dental drills |
Corrosion resistance, smooth operation |
Semiconductor and Electronics |
Semiconductor manufacturing equipment, electronics devices |
High precision, low friction |
Automotive and Aerospace |
Automotive components, aerospace bearings |
Reduced weight, improved fuel efficiency, increased performance |
Industrial Machinery |
Pumps, compressors, conveyors |
Durability, corrosion resistance |