Thrust Needle Roller Bearings: A Comprehensive Guide to Design, Maintenance, and Benefits
Thrust needle roller bearings are a type of rolling-element bearing designed to withstand high axial loads while allowing for minimal rotation. These bearings are composed of precisely engineered cylindrical needle rollers, a thrust washer, and a housing. They are commonly utilized in various applications such as automotive transmissions, industrial gearboxes, and wind turbines.
Understanding Thrust Needle Roller Bearings
Design and Operation
Thrust needle roller bearings consist of a set of needle rollers arranged radially within a hardened steel housing. The rollers are kept in place by a thrust washer, typically manufactured from a polymer material. As an axial load is applied to the bearing, the rollers roll between the thrust washer and the bearing housing, facilitating smooth rotational motion.
Advantages of Thrust Needle Roller Bearings
-
High Load Capacity: Thrust needle roller bearings excel in withstanding heavy axial loads due to the large contact area between the rollers and the bearing raceway.
-
Low Friction: The rolling motion of the needle rollers minimizes friction, resulting in efficient operation and extended bearing life.
-
Compact Design: Thrust needle roller bearings offer a compact design, making them suitable for applications with space constraints.
-
High Speed Capability: These bearings can accommodate high rotational speeds, enabling their use in demanding applications.
-
Easy Maintenance: Thrust needle roller bearings require minimal maintenance, reducing downtime and maintenance costs.
Selection and Application of Thrust Needle Roller Bearings
Factors to Consider
When selecting a thrust needle roller bearing, several factors need to be taken into account:
-
Load Capacity: Determine the axial load the bearing will be subjected to.
-
Speed: Consider the maximum rotational speed at which the bearing will operate.
-
Radial Clearance: Select an appropriate radial clearance to allow for thermal expansion and misalignment.
-
Operating Environment: Consider the temperature, lubrication, and contamination conditions of the bearing application.
Common Applications
Thrust needle roller bearings find applications in a wide range of industries and equipment, including:

- Automotive transmissions
- Machine tools
- Gearboxes
- Wind turbines
- Medical devices
- Aerospace components
Maintenance of Thrust Needle Roller Bearings
To ensure optimal performance and longevity, regular maintenance is crucial for thrust needle roller bearings:
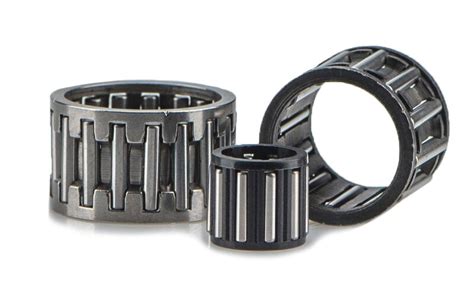
-
Lubrication: Use the recommended lubricant type and quantity to reduce friction and wear.
-
Bearing Inspection: Regularly inspect the bearing for damage, wear, or contamination.
-
Replacement: Replace worn or damaged bearings promptly to prevent catastrophic failure.
Common Mistakes to Avoid
-
Overloading: Avoid exceeding the specified load capacity of the bearing.
-
Improper Lubrication: Use the correct lubricant type and quantity to prevent bearing failure.
-
Misalignment: Ensure proper alignment between the bearing and the shaft to prevent premature wear.
-
Ignoring Maintenance: Regular maintenance is essential to maximize bearing life and prevent costly repairs.
Step-by-Step Approach to Thrust Needle Roller Bearing Maintenance
-
Inspect the bearing for damage, wear, or contamination.
-
Clean the bearing thoroughly using an appropriate solvent.
-
Apply lubricant to the bearing surfaces according to the manufacturer's recommendations.
-
Reinstall the bearing into its housing, ensuring proper alignment.
Why Thrust Needle Roller Bearings Matter
Thrust needle roller bearings play a critical role in various applications:

-
Power Transmission: In automotive transmissions, thrust needle roller bearings transmit power from the engine to the wheels.
-
Load Support: In machine tools, they support heavy axial loads during machining operations.
-
Speed Control: In wind turbines, thrust needle roller bearings help control the rotational speed of the turbine blades.
-
Precision Positioning: In medical devices, they enable precise positioning of surgical tools.
Benefits of Using Thrust Needle Roller Bearings
-
Increased Efficiency: Reduced friction leads to improved efficiency and lower energy consumption.
-
Extended Bearing Life: Proper maintenance and lubrication extend bearing life, reducing downtime and replacement costs.
-
Enhanced Load Capacity: High load capacity enables these bearings to withstand demanding operating conditions.
-
Compact Size: The compact design allows for space optimization in various applications.
Table 1: Typical Specifications of Thrust Needle Roller Bearings
Specification |
Value |
Load Capacity |
Up to 100,000 lbs |
Speed Capacity |
Up to 100,000 RPM |
Operating Temperature Range |
-40°F to 250°F |
Radial Clearance |
0.0002 to 0.001 in |
Table 2: Common Applications of Thrust Needle Roller Bearings
Industry |
Application |
Automotive |
Transmissions, differentials |
Industrial |
Gearboxes, machine tools |
Aerospace |
Jet engines, aircraft control systems |
Medical |
Surgical instruments, robotics |
Table 3: Troubleshooting Tips for Thrust Needle Roller Bearings
Symptom |
Possible Cause |
Solution |
Premature bearing failure |
Overloading, improper lubrication, contamination |
Reduce load, use appropriate lubricant, clean bearing |
Excessive noise or vibration |
Misalignment, bearing damage |
Realign bearing, replace damaged components |
High operating temperature |
Inadequate lubrication, bearing damage |
Increase lubrication, inspect for wear |
FAQs
- What is the difference between thrust needle roller bearings and radial needle roller bearings?
- Thrust needle roller bearings withstand axial loads, while radial needle roller bearings handle radial loads.
- How do I determine the correct thrust needle roller bearing size for my application?
- Refer to the manufacturer's specifications or consult an engineering professional.
- Can thrust needle roller bearings operate without lubrication?
- No, lubrication is essential to minimize friction and prevent bearing failure.
- How often should I inspect thrust needle roller bearings?
- Regular inspection intervals depend on the operating conditions, but generally, monthly or quarterly inspections are recommended.
- Can I extend the life of thrust needle roller bearings?
- Yes, proper lubrication, alignment, and maintenance can significantly enhance bearing life.
Call to Action
Thrust needle roller bearings offer exceptional performance and reliability in various applications. By understanding their design, application, and maintenance requirements, you can optimize their performance and extend their operating life. Contact your bearing supplier today to learn more about thrust needle roller bearings and how they can benefit your equipment.