The Essential Guide to Needle Bearing Pullers: Removal, Installation, and Maintenance
Needle bearing pullers play a crucial role in the maintenance and repair of various industrial machinery, automotive components, and precision devices. These specialized tools are designed to safely and efficiently remove and install needle bearings, which are cylindrical roller bearings that are widely used in applications requiring high speed and low friction.
Understanding Needle Bearings and their Applications
Needle bearings are characterized by their small diameter and long, slender rollers. This unique design allows them to handle significant radial loads while maintaining a low profile and reduced friction. They are commonly found in:
- Automotive transmissions and differentials
- Machine tool spindles
- Power tools
- Robotics
- Precision instruments
Types of Needle Bearing Pullers
Needle bearing pullers come in a variety of designs to accommodate different bearing sizes and applications. The two main types include:

-
Hydraulic Needle Bearing Pullers: These pullers utilize hydraulic pressure to generate a powerful force that evenly distributes the load around the bearing race. They are suitable for removing stubborn or seized bearings.
-
Mechanical Needle Bearing Pullers: These pullers employ mechanical leverage to apply a gradual force to the bearing race. They are commonly used for smaller bearings and in applications where hydraulics are not feasible.
Essential Features of a Needle Bearing Puller
When choosing a needle bearing puller, consider the following key features:
-
Capacity: The puller should have sufficient capacity to handle the size and type of bearings being removed or installed.
-
Versatility: The puller should be adaptable to different bearing sizes and applications.
-
Durability: The puller should be made of high-quality materials and be able to withstand repeated use.
-
Ease of Use: The puller should be easy to assemble, use, and disassemble.
-
Safety Features: The puller should incorporate safety features to prevent injury or damage during operation.
Safe and Effective Use of Needle Bearing Pullers
To ensure the safe and effective use of needle bearing pullers, follow these best practices:
-
Inspect the Puller: Before using the puller, inspect it thoroughly to ensure that it is in good working condition and free of damage.
-
Choose the Right Puller: Select the appropriate puller for the size and type of bearing being removed or installed.
-
Secure the Workpiece: Stabilize the workpiece to prevent movement during the pulling or installation process.
-
Apply Force Gradually: Apply force to the puller steadily and gradually to minimize the risk of damage to the bearing or the workpiece.
-
Inspect the Bearing: After removal or installation, inspect the bearing and the puller for any signs of damage or wear.
-
Store Properly: Clean and store the puller in a dry and safe location to prevent corrosion or damage.
Effective Strategies for Successful Needle Bearing Pulling and Installation
-
Use a Suitable Puller: Select a puller that is specifically designed for removing or installing needle bearings.
-
Lubricate the Race: Apply a thin layer of lubricant to the bearing race to reduce friction and prevent damage.
-
Secure the Bearing: Center the puller claws on the bearing race and tighten them securely to ensure a firm grip.
-
Apply Steady Force: Use a hydraulic pump or mechanical lever to apply force to the puller. Increase the force gradually to avoid excessive stress on the bearing or the workpiece.
-
Monitor the Process: Observe the bearing as it is being removed or installed. If you encounter any resistance or abnormalities, stop the process and consult the manufacturer's instructions.
Common Mistakes to Avoid When Using Needle Bearing Pullers
-
Overtightening the Puller Claws: Excessive tightening can damage the bearing race or cause the claws to slip.
-
Applying Abrupt Force: Jerking or hammering the puller can shock the bearing and lead to damage.
-
Using a Puller that is Not Suitable for the Bearing: Using an inappropriate puller can result in injury, damage to the bearing, or failure to remove or install the bearing effectively.
-
Ignoring Lubrication: Neglecting to lubricate the bearing race can increase friction and cause premature wear or damage.
-
Not Inspecting the Puller or Bearing: Failure to inspect the puller or the bearing before and after use can lead to accidents or damage.
Step-by-Step Approach to Removing and Installing Needle Bearings
Removal:

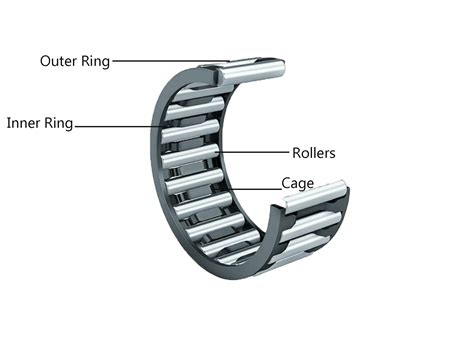
- Choose the correct needle bearing puller for the bearing size and application.
- Secure the workpiece in a vise or on a stable surface.
- Lubricate the bearing race with a suitable lubricant.
- Position the puller claws on the bearing race and tighten them securely.
- Apply force to the puller using a hydraulic pump or mechanical lever.
- Gradually increase the force until the bearing is removed.
Installation:
- Clean the bearing bore to remove any debris or dirt.
- Apply a thin layer of lubricant to the bearing bore.
- Position the bearing in the bore and align it correctly.
- Place the needle bearing puller over the bearing.
- Secure the puller claws on the bearing race and tighten them evenly.
- Apply force to the puller using a hydraulic pump or mechanical lever.
- Gradually increase the force until the bearing is fully seated in the bore.
Pros and Cons of Needle Bearing Pullers
Pros:
- Efficient and safe removal and installation of needle bearings
- Versatile and adaptable to different bearing sizes and applications
- Durable and designed to withstand repeated use
- Utilizes mechanical leverage or hydraulic pressure for precise force application
Cons:
- Specialized tools that require specific knowledge and training to operate effectively
- Can be expensive to purchase, especially for high-capacity hydraulic models
- May not be suitable for all types of bearings or bearing arrangements
- Requires proper maintenance and care to ensure optimal performance
Frequently Asked Questions (FAQs)
-
What is the difference between a hydraulic and mechanical needle bearing puller?
- Hydraulic needle bearing pullers use hydraulic pressure to generate a powerful force, while mechanical needle bearing pullers use mechanical leverage to apply a gradual force.
-
What safety precautions should be taken when using a needle bearing puller?
- Inspect the puller and bearing before and after use, secure the workpiece to prevent movement, and apply force gradually to avoid damage or injury.
-
How can I choose the right needle bearing puller for my application?
- Consider the size and type of bearing being removed or installed, the capacity and versatility of the puller, and the ease of use and safety features.

-
What are some effective strategies for successful needle bearing pulling and installation?
- Use a suitable puller, lubricate the race, secure the bearing, apply steady force, and monitor the process.
-
What common mistakes should I avoid when using a needle bearing puller?
- Overtightening the puller claws, applying abrupt force, using an unsuitable puller, ignoring lubrication, and not inspecting the puller or bearing.
-
How do I properly remove a needle bearing using a needle bearing puller?
- Secure the workpiece, lubricate the race, position the puller claws, tighten them securely, and apply force gradually using a hydraulic pump or mechanical lever.
-
How do I install a needle bearing using a needle bearing puller?
- Clean the bore, lubricate it, position the bearing, place the puller over the bearing, secure the claws, and apply force gradually using a hydraulic pump or mechanical lever.
-
What are the advantages and disadvantages of using a needle bearing puller?
- Advantages include efficient removal and installation, versatility, durability, and precise force application. Disadvantages include specialized tools requiring specific knowledge and training, potential expense, and limitations for certain bearing types or arrangements.