Industrial Robot Primer: Empowering Industries with Precision and Efficiency
Introduction
Industrial robots are transforming manufacturing, logistics, and other industries by automating tasks with unparalleled precision and efficiency. These versatile machines enhance productivity, reduce costs, and improve workplace safety. This primer provides a comprehensive guide to industrial robotics, exploring their capabilities, applications, and the latest advancements.
Types of Industrial Robots
Industrial robots come in various types, each designed for specific applications:
-
Articulated robots have flexible arms with multiple joints, enabling complex movements and precise positioning.
-
SCARA robots (Selective Compliance Assembly Robot Arm) are ideal for assembly tasks that require high-speed and precision.
-
Parallel robots have multiple arms connected by parallel links, offering fast and accurate movements.
-
Collaborative robots (cobots) work safely alongside human workers, enhancing productivity without compromising safety.
Applications of Industrial Robots
Industrial robots find applications in a wide range of industries:
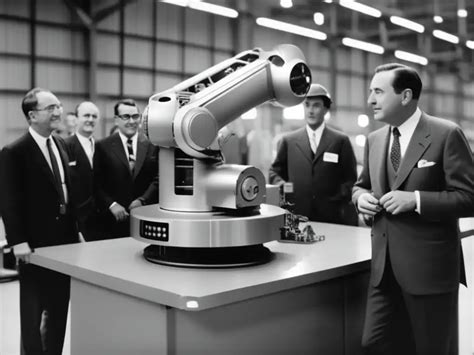
-
Manufacturing: Welding, assembly, painting, and material handling
-
Logistics: Warehousing, order fulfillment, and transportation
-
Medical: Surgery, diagnostics, and drug discovery
-
Agriculture: Harvesting, sorting, and processing produce
-
Construction: Building, welding, and material handling
Benefits of Industrial Robots
Industrial robots offer numerous benefits:

-
Increased productivity: Robots can operate continuously, reducing lead times and boosting output.
-
Improved quality: Robots ensure consistent accuracy, leading to fewer defects and enhanced product quality.
-
Reduced labor costs: Robots can automate repetitive tasks, freeing up human workers for higher-value activities.
-
Workplace safety: Robots can perform hazardous or heavy tasks, reducing the risk of accidents and injuries.
-
Sustainability: Robots can optimize resource consumption, reducing waste and minimizing environmental impact.
Key Features to Consider When Choosing an Industrial Robot
When selecting an industrial robot, consider the following key features:
-
Payload capacity: The maximum weight the robot can handle.
-
Reach: The distance the robot can extend its arm.
-
Accuracy: The ability of the robot to perform tasks with precision.
-
Speed: The rate at which the robot can execute movements.
-
Environmental protection: The robot's ability to withstand specific environmental conditions, such as temperature, humidity, and dust.
Industry Trends and Future Outlook
The industrial robotics industry is rapidly evolving:
-
Cobots gaining popularity: Cobots are becoming increasingly popular due to their ease of integration and ability to work safely with humans.
-
Artificial intelligence (AI): AI-powered robots are improving their decision-making capabilities and adaptability to complex environments.
-
IoT (Internet of Things): Connecting robots to the IoT enables data exchange and real-time monitoring, enhancing efficiency and predictive maintenance.
-
Increased demand for industrial robots: The global demand for industrial robots is projected to reach $60 billion by 2024, driven by growing automation adoption.
Case Studies
Case Study 1: Increased Productivity in Automotive Manufacturing
In a major automotive manufacturing plant, the integration of industrial robots for welding tasks resulted in a 30% increase in productivity. The robots operated 24/7, ensuring continuous production and reducing lead times.
Case Study 2: Enhanced Precision in Medical Surgery
In a leading medical facility, a collaborative robot was deployed for surgical procedures. The robot's precision and steady hand movements improved surgical outcomes, reducing the risk of complications.

Case Study 3: Improved Safety in Warehousing
In a large-scale distribution center, the implementation of mobile robots for material handling eliminated the need for manual lifting and transportation. This significantly reduced workplace accidents and injuries.

Best Practices for Industrial Robot Implementation
To ensure successful implementation of industrial robots, consider the following best practices:
-
Conduct a thorough needs assessment: Identify the specific tasks and requirements for which robots are needed.
-
Choose the right type of robot: Select a robot that meets the payload, reach, accuracy, speed, and environmental protection requirements.
-
Provide proper training: Train personnel on operating, maintaining, and programming the robots safely and effectively.
-
Integrate with existing systems: Ensure smooth communication and data exchange between robots and other systems, such as PLCs and MES (Manufacturing Execution Systems).
-
Implement regular maintenance: Schedule regular maintenance and inspections to keep the robots operating at optimal performance.
Common Mistakes to Avoid
Avoid these common mistakes when implementing industrial robots:
-
Overestimating capabilities: Carefully assess the limitations of robots and ensure they are not tasked with functions beyond their capabilities.
-
Insufficient training: Inadequate training can lead to improper operation, errors, and safety hazards.
-
Ignoring safety measures: Prioritize safety by installing proper guarding, implementing risk assessments, and providing adequate training.
-
Lack of integration planning: Poor integration with existing systems can lead to communication issues and reduced efficiency.
-
Underestimating maintenance requirements: Neglecting maintenance can lead to equipment failure and costly downtime.
How to Choose the Best Industrial Robot for Your Needs
Follow these steps to select the best industrial robot for your requirements:
-
Define your application: Clearly outline the specific tasks and goals you want the robot to perform.
-
Research different types of robots: Explore the various types of robots available and their suitability for your application.
-
Determine key specifications: Identify the payload capacity, reach, accuracy, speed, and environmental protection requirements.
-
Consider industry trends: Research the latest advancements in industrial robotics to ensure you invest in a robot that aligns with future trends.
-
Consult with experts: Seek guidance from robot manufacturers, system integrators, or industry professionals to make an informed decision.
Potential Drawbacks of Industrial Robots
Consider these potential drawbacks before implementing industrial robots:
-
High initial investment: Industrial robots can be expensive to purchase, install, and maintain.
-
Job displacement: Robots can automate tasks that were previously performed by human workers, potentially leading to job losses.
-
Safety concerns: Improper installation, operation, or maintenance of robots can pose safety risks to humans.
-
Limited flexibility: Robots are programmed to perform specific tasks, which may limit their applicability in highly variable environments.
-
Lack of creativity: Robots are not capable of human-like creativity and problem-solving abilities.
Pros and Cons of Industrial Robots
Consider the following pros and cons before investing in industrial robots:
Pros:
-
Increased productivity: Robots can operate continuously, improving output and efficiency.
-
Reduced labor costs: Robots can automate repetitive tasks, freeing up human workers for higher-value activities.
-
Improved quality: Robots ensure consistent accuracy, leading to fewer defects and enhanced product quality.
-
Workplace safety: Robots can perform hazardous or heavy tasks, reducing the risk of accidents and injuries.
-
Sustainability: Robots can optimize resource consumption, reducing waste and minimizing environmental impact.
Cons:
-
High initial investment: Industrial robots can be expensive to purchase, install, and maintain.
-
Job displacement: Robots can automate tasks that were previously performed by human workers, potentially leading to job losses.
-
Safety concerns: Improper installation, operation, or maintenance of robots can pose safety risks to humans.
-
Limited flexibility: Robots are programmed to perform specific tasks, which may limit their applicability in highly variable environments.
-
Lack of creativity: Robots are not capable of human-like creativity and problem-solving abilities.
Conclusion
Industrial robots are transforming industries with their ability to enhance productivity, precision, and safety. By carefully considering the types, applications, benefits, and drawbacks of industrial robots, you can make informed decisions about their implementation and reap the benefits of their technological advancements. Embracing industrial robotics is crucial for businesses looking to stay competitive and drive innovation in the digital age.
References