Industrial Robot Welding: Revolutionizing Manufacturing with Precision and Efficiency
Introduction
Industrial robot welding has emerged as a transformative technology within the manufacturing industry, redefining precision, efficiency, and the future of production. With its ability to automate complex welding processes, robots have enabled manufacturers to achieve unprecedented levels of quality, consistency, and productivity.
Benefits of Industrial Robot Welding
The advantages of industrial robot welding are undeniable:
-
Enhanced Precision: Robots excel in repetitive tasks with unwavering accuracy, minimizing human error and ensuring consistent weld quality.
-
Increased Efficiency: Automation reduces the time required for welding operations, freeing up human workers for higher-level tasks.
-
Improved Safety: Robots eliminate the exposure of human workers to hazardous fumes, sparks, and molten metal.
-
Lower Costs: Over the long term, robot welding can significantly reduce labor costs, maintenance expenses, and rework rates.
-
Increased Productivity: Automated welding processes operate 24/7, maximizing production output and reducing lead times.
Statistical Evidence of Benefits
According to the International Federation of Robotics (IFR), the global market for industrial robots is projected to grow to $85 billion by 2026. This exponential growth is driven by the increasing adoption of robotics in welding applications, as manufacturers strive to enhance their competitiveness.

Types of Industrial Welding Robots
Industrial welding robots come in various types to cater to different welding requirements:
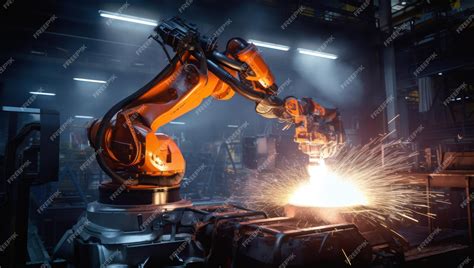
-
Arc Welding Robots: These robots use an electric arc to melt the metal and create a weld.
-
Spot Welding Robots: They apply pressure and electric current to two metal sheets, creating a spot weld.
-
Laser Welding Robots: Employing a laser beam, these robots produce high-precision welds with minimal distortion.
-
Resistance Welding Robots: Utilize high-frequency electric current to create a weld between two metal surfaces.
-
Hybrid Welding Robots: Combine different welding techniques to achieve optimal results in specific applications.
Applications of Industrial Robot Welding
Industrial robot welding finds applications across a wide range of industries:
-
Automotive: Body assembly, welding of engine components, and exhaust systems.
-
Aerospace: Welding of aircraft parts, including wings, fuselages, and landing gear.
-
Construction: Fabrication of structural steel buildings, bridges, and heavy equipment.
-
Shipbuilding: Welding of hulls, decks, and superstructures.
-
Energy: Construction of pipelines, wind turbines, and power plants.
Case Study: Automotive Industry
In the automotive industry, industrial robot welding is revolutionizing assembly lines. Ford Motor Company, for example, has deployed over 1,400 welding robots in its Louisville Assembly Plant. These robots have significantly improved welding accuracy, reduced assembly time by 15%, and cut down on the number of defective vehicles.
Effective Strategies for Implementing Industrial Robot Welding
To maximize the benefits of industrial robot welding, consider the following strategies:
-
Thorough Planning: Conduct a comprehensive analysis of welding requirements, identify suitable robot types, and optimize the welding process.
-
Appropriate Robot Selection: Choose robots that match the specific welding needs, considering factors such as payload capacity, reach, and accuracy.
-
Skilled Workforce: Train and upskill employees to operate and maintain the robots effectively.
-
Safety First: Implement safety protocols, including proper guarding, training, and regular inspections.
-
Regular Maintenance: Schedule preventive maintenance to ensure optimal robot performance and extend its lifespan.
Tips and Tricks for Successful Industrial Robot Welding
-
Optimize Welding Parameters: Experiment with different welding variables, such as travel speed, wire feed rate, and shielding gas, to find the optimal settings for each application.
-
Use High-Quality Welding Consumables: Select high-quality wire, shielding gas, and electrodes to ensure reliable welds.
-
Properly Clean and Prepare Workpieces: Clean and prepare workpieces thoroughly before welding to minimize weld defects and improve weld quality.
-
Monitor and Inspect Welds: Regularly monitor and inspect welds using non-destructive testing methods to ensure integrity.
-
Continuous Improvement: Engage in ongoing performance analysis and feedback to identify areas for improvement and optimize the welding process.
Common Mistakes to Avoid in Industrial Robot Welding
-
Insufficient Planning: Inadequate planning can lead to improper robot selection, suboptimal process design, and poor implementation.
-
Improper Maintenance: Neglecting preventive maintenance can result in robot breakdowns, production delays, and costly repairs.
-
Lack of Training: Insufficiently trained operators increase the risk of accidents, incorrect setup, and poor weld quality.
-
Inadequate Safety Measures: Overlooking safety protocols can compromise worker safety and increase the likelihood of incidents.
-
Ignoring Weld Quality Control: Failing to monitor and inspect welds regularly can result in undetected defects and potential product failures.
Why Industrial Robot Welding Matters
Industrial robot welding matters because it:


-
Enhances Product Quality: Robots provide consistent and precise welds, reducing defects and improving the overall quality of manufactured products.
-
Increases Productivity: Automation frees up human workers for value-added tasks, boosting productivity and reducing lead times.
-
Lowers Manufacturing Costs: In the long run, robot welding reduces labor expenses, material waste, and rework costs, leading to increased profitability.
-
Improves Worker Safety: Removing humans from hazardous welding environments minimizes the risk of accidents and occupational diseases.
-
Enhances Competitiveness: By adopting robot welding, manufacturers can remain competitive in a rapidly evolving global market and meet the demands of modern consumers.
Potential Drawbacks of Industrial Robot Welding
Despite its numerous benefits, industrial robot welding also has some potential drawbacks:
-
Initial Investment: Acquiring and implementing industrial robots requires a significant initial investment, which may be challenging for smaller businesses.
-
Technical Complexity: Programming and operating industrial robots require specialized skills and training, which can be a barrier for companies with limited technical capabilities.
-
Potential Job Displacement: The automation of welding tasks may lead to job displacement for unskilled workers, requiring retraining and upskilling initiatives.
-
Maintenance and Repairs: Industrial robots require regular maintenance and repairs, which can add to the operating costs over time.
-
Limited Flexibility: Robots are programmed to perform specific welding tasks, and reprogramming them for different applications can be time-consuming and expensive.
Call to Action
If you are considering implementing industrial robot welding in your manufacturing operations, it is essential to conduct thorough research, plan effectively, and select a reputable robot supplier. By leveraging the benefits of robot welding, you can unlock significant gains in quality, productivity, safety, and cost savings. Embrace the power of automation to drive your manufacturing business to new heights of success.
Humorous Stories and Lessons Learned
-
The Robot's Revenge: A welding robot malfunctioned and inadvertently welded a worker's tools to his workbench. Lesson learned: Always ensure proper safety protocols and regular robot maintenance.
-
The Dancing Robot: A robot welder programmed with incorrect parameters comenzó a dance around the workpiece, creating a completely distorted weld. Lesson learned: Thoroughly test and verify all welding parameters before initiating the welding process.
-
The Missing Weld: A robot welder skipped an important weld joint, leaving a critical part of the assembly dangerously compromised. Lesson learned: Implement robust quality control measures and conduct regular weld inspections.